Sustainability Policy
Preserving our Environment
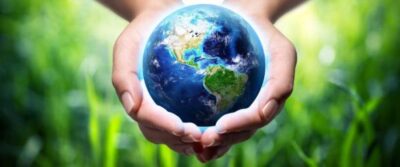
The ASP Access Floors Sustainability Policy outlines how ASP endeavors to use recycled materials and reduce greenhouse gas and carbon emissions.
The implementation of the Sustainability will ensure ASP :
- Considers sustainability in all relevant decision making
- Reduce their greenhouse gas emissions
- Produce less waste and increase recycling
The aim of this policy is to incorporate ecologically sustainable development principles in every facet of design, manufacturing, logistics and installation with the introduction of the following key objectives :
- Indoor Environment Quality
- Waste Management
- Recycled Content
- Life Cycle Analysis and Environmental Product Declaration
Section 1: Indoor Environment Quality
Objective: ASP ensures that our VOC content on our pedestal adhesive and concrete slab sealer is in line with the Green Building Council Requirements.
Solution: All ASP adhesives are water-based and so are nontoxic. The Green Building Council requirement is not more than 50g/kg VOC for sealants and adhesives. The ASP test data concludes that the nominated pedestal glue and concrete sealer are both under the recommended 50g/kg. Please find VOC datasheets attached at the rear of the policy.
Section 2: Waste Management
Objective: ASP Access Floors aims to minimise the waste material produced on each project.
Solution: ASP Access Floors offers their waste minimisation perimeter floor installation system. This system maximises the usable amount of cut panels around the perimeter hence minimising the waste material.
Section 3: Recycled Content
Objective: ASP Access Floors aims to produce access floor panels with a high percentage of recycled material.
Solution: The recycled content data sheet can be found attached to the rear of the sustainability policy.
Section 4: Life Cycle Analysis and Environmental Product Declaration
Objective: To conduct LCA study, compile an EPD and obtain verification
Solution: In life cycle assessment, an Environmental Product Declaration (EPD) is a standardized way of quantifying the environmental impact of a product or system.
Step 1. ASP conduct an LCA according to ISO 14 040-44 standards.
Step 2. Develop the EPD
- Develop EPD document including LCA results and the product description
- Develop a Project Verification Report (PVR)
Step 3. Verification and registration.
A third party expert verifies:
- The EPD document
- The PVR
- The LCA study
- And files a Verification Report
Registration with the EPD programme operator
- The EPD document, the Verification Report, the registration form and a short description of ASP Access Floor is filed and signed off by the EPD programme operator